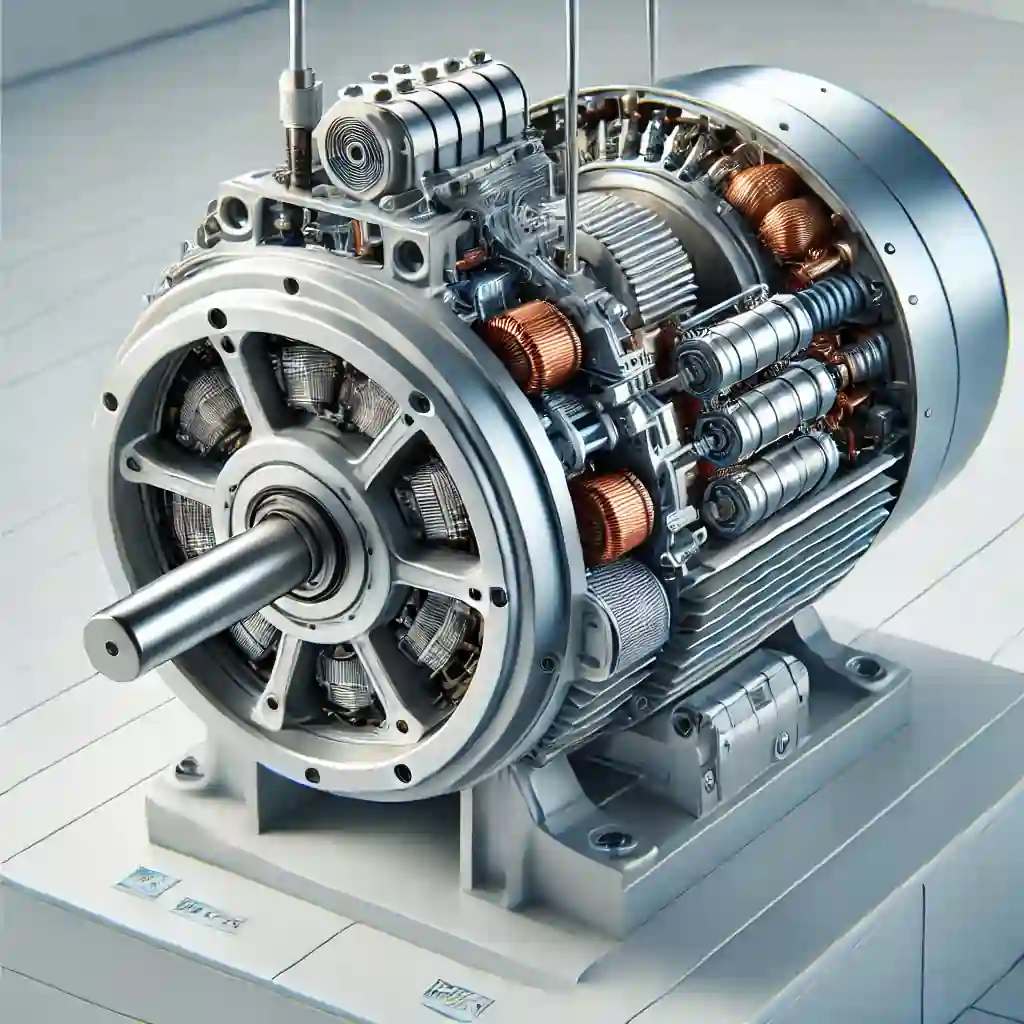
Table of Contents
Why Does Heating Occur in a Motor?
Many might assume that continuous operation, such as running a motor 24/7 in a plant, is the main cause of overheating. However, if a motor operates within its rated capacity, prolonged operation alone does not lead to overheating. Let’s explore the key factors behind motor heating.
Introduction: Debunking the Myth of Continuous Operation
Imagine a factory floor where motors hum tirelessly, powering conveyor belts, pumps, and machinery 24/7. A common assumption is that these motors overheat because they never stop running. However, the reality is more nuanced. Motors are engineered to operate continuously within their rated capacity. If they overheat under such conditions, the root cause is rarely the runtime itself—it’s almost always a symptom of deeper inefficiencies, design flaws, or external factors.
This article explores the science behind motor heating, unraveling the myths and explaining the unavoidable physics, environmental challenges, and maintenance pitfalls that lead to temperature rise. Whether you’re an engineer, a plant manager, or simply curious about how motors work, this guide will equip you with actionable insights to diagnose, prevent, and address overheating.
Misconceptions About Motor Heating
1. Running Below Rated Load
A motor operating below its rated load should not overheat. For example:
- If a motor has a full-load capacity of 20 amperes but operates at 12 amperes, it shouldn’t overheat as it is functioning below its rated capacity.
2. Environmental Factors
- Dust accumulation can impact cooling by insulating the motor and preventing efficient heat dissipation.
- In clean and dust-free environments, overheating cannot typically be attributed to dust.
So, what actually causes motor heating?
Energy Conversion and Efficiency
The primary role of a motor is to convert electrical energy into mechanical energy. However, this energy conversion is not 100% efficient. For example:
- A motor with an efficiency of 90% loses 10% of the electrical energy as heat.
The Physics of Motor Heating – Energy Conversion Isn’t Perfect
At its core, a motor converts electrical energy into mechanical energy. But this process isn’t 100% efficient. Even the best motors waste some energy as heat due to inherent physical limitations. Let’s break this down:
Energy Efficiency: The Starting Point
A motor’s efficiency rating (e.g., 90%) tells you how much electrical energy becomes useful mechanical work. The remaining 10% is lost—mostly as heat. For example:
- A 100-horsepower motor with 95% efficiency draws ~78 kW of electrical power.
- Of this, ~3.9 kW is lost as heat.
This heat must be dissipated to avoid damage.
The Four Types of Losses That Generate Heat
Heating in motors stems from four primary sources, each tied to the motor’s design and operation:
1. Copper Losses (I²R Losses)
- What Happens: Current flowing through the motor’s windings (usually copper) encounters resistance. Heat is generated proportionally to the square of the current (I²) multiplied by resistance (R).
- Example: A motor drawing 20 amps with a winding resistance of 0.1 ohms produces 40 watts of heat (20² × 0.1).
- The Vicious Cycle: As temperatures rise, copper’s resistance increases by ~0.4% per °C. This raises I²R losses further, creating a feedback loop.
2. Iron Losses (Core Losses)
- What Happens: Alternating current in the stator creates a magnetic field that reverses direction constantly. This hysteresis (lag) and eddy currents in the iron core generate heat.
- Impact: Iron losses are significant in motors running at partial load or with poor-quality laminations.
3. Mechanical Losses
- Friction in bearings, brushes (in DC motors), and air resistance from rotating parts (windage) contribute to heat.
- Case Study: A paper mill reduced bearing-related failures by 60% after switching to sealed, lubricated bearings.
4. Stray Load Losses
- Less predictable losses from magnetic leakage, harmonics, or imperfect manufacturing.
Environmental and Operational Factors – Beyond the Motor’s Design
Even a well-designed motor can overheat if external conditions aren’t managed.
1. Ambient Temperature and Ventilation
- Motors rely on ambient air for cooling. In a 40°C environment, a motor’s safe operating temperature is effectively reduced.
- Rule of Thumb: For every 10°C above rated ambient temperature, insulation life halves.
2. Dust and Contaminants
- Dust coats surfaces, acting as an insulator. A study by the Electrical Apparatus Service Association (EASA) found that dust buildup can reduce cooling efficiency by 20–40%.
- Real-World Example: A cement plant saw motor failures drop by 70% after installing air filters in motor enclosures.
3. Altitude Effects
- At high altitudes, thinner air reduces convective cooling. Motors derated for altitude (e.g., -3% capacity per 1,000 feet above 3,300 ft) are often overlooked.
The Cooling System – Your Motor’s Lifeline
Most motors use an integrated cooling fan to dissipate heat. But this system is vulnerable:
How It Works:
- A fan mounted on the rotor shaft blows air over the motor’s frame.
- Key Insight: If the fan fails (e.g., due to debris or bearing wear), temperatures can spike by 50–100°C within minutes.
Case Study: Cooling Fan Failure in a HVAC System
A shopping mall’s air handling unit motor failed catastrophically when a plastic bag blocked the cooling fan. Post-failure analysis showed winding temperatures exceeded 150°C, melting insulation.
Consequences of Overheating – More Than Just a Shutdown
Unchecked heating triggers a domino effect:
- Insulation Degradation: Modern motors use Class F or H insulation (rated for 155°C or 180°C). Prolonged overheating causes brittleness and cracks.
- Bearing Failure: Heat expands metal components, increasing friction and accelerating wear.
- Demagnetization (PMSM Motors): Permanent magnets lose strength at high temperatures.
Preventing Overheating – Strategies That Work
1. Operational Best Practices
- Avoid frequent starts/stops (induction motors draw 6x rated current at startup).
- Use variable frequency drives (VFDs) to match motor speed to load, reducing losses.
2. Maintenance Must-Dos
- Clean cooling fins and vents regularly.
- Monitor bearing temperatures with infrared cameras.
- Check voltage imbalance (a 3.5% imbalance increases losses by 25%).
3. Design Upgrades
- Premium efficiency (IE3/IE4) motors reduce losses by 15–40%.
- Liquid-cooled motors for extreme environments.
Conclusion: Knowledge is Power (and Cooler Motors)
Motor heating isn’t an inevitability—it’s a manageable challenge. By understanding the interplay of physics, environment, and maintenance, you can extend motor life, reduce downtime, and save energy. Next time you hear a motor humming, remember: its temperature tells a story. With the right tools and knowledge, you can ensure it’s a story of reliability, not failure.
FAQS
-
Can a motor run non-stop without overheating?
Yes—if it operates within its rated load, voltage, and ambient temperature. Motors are designed for continuous duty, but only under specified conditions. For example, a 10-horsepower motor running at 7 horsepower in a clean, cool environment can operate indefinitely. Overheating arises when external factors (e.g., blocked cooling, voltage imbalance) or internal inefficiencies (e.g., worn bearings) push it beyond design limits
-
Why aren’t motors 100% efficient?
Physics! Energy conversion inherently involves losses:
Copper losses: Resistance in windings generates heat (I²R).
Iron losses: Magnetic hysteresis and eddy currents in the core.
Friction and windage: Mechanical resistance in bearings and airflow.
Even premium IE4 motors max out at ~97% efficiency. The remaining 3% is lost as heat. -
What are the first signs of motor overheating?
Watch for:
Unusual smells: Burning insulation (a pungent, acrid odor).
Noise: Grinding (bearing failure) or humming (voltage issues).
Tripped breakers: Overloads from excessive current draw.
Hot surfaces: Use an infrared thermometer—surface temps above 90°C (194°F) often indicate trouble. -
Does ambient temperature really matter?
Yes. Motors are rated for specific ambient temps (usually 40°C or 104°F). For every 10°C above this:
Insulation life halves (per the Arrhenius rate rule).
Efficiency drops by ~1–2% due to increased resistance.
In desert climates or foundries, opt for high-temp insulation (Class H) or liquid cooling.
-
Can dust or dirt really cause overheating?
Absolutely. Dust acts like a blanket, trapping heat. A study by EASA found:
A 1/16-inch dust layer on motor surfaces can reduce cooling efficiency by 20%.
In textile mills, motors clogged with lint failed 3x faster than cleaned ones.
Solution: Use IP55-rated enclosures in dusty environments and clean vents quarterly. -
Why does voltage imbalance cause heating?
A 3.5% voltage imbalance between phases creates:
Negative sequence currents: These induce opposing magnetic fields, forcing the motor to work harder.
Result: Losses increase by up to 25%, per IEEE standards.
Fix: Install phase monitors and balance loads across all three phases. -
How do I know if my motor is within safe temperatures?
Use these tools:
Infrared thermometers: Check surface temps (stay below 90°C).
Thermal imaging cameras: Spot hotspots in windings or bearings.
Embedded sensors: Modern motors have RTDs (resistance temperature detectors) for real-time monitoring. -
Can frequent starts/stops cause heating?
Yes. Each start surges current (6x rated amps in induction motors), causing:
Rapid copper loss buildup.
Mechanical stress on windings and bearings.
Rule of Thumb: Limit starts to 4–6 per hour for standard motors. Use soft starters or VFDs to reduce inrush currents. -
Should I repair or replace an overheated motor?
: It depends:
Repair if: Only bearings or cooling fans are damaged, and windings test OK with a megohmmeter (>100 MΩ resistance).
Replace if: Windings are charred, insulation is cracked, or the rotor is warped (costs often exceed 60% of a new motor).
Expert Opinion: The Electrical Apparatus Service Association (EASA) recommends replacement after severe overheating due to hidden insulation damage.